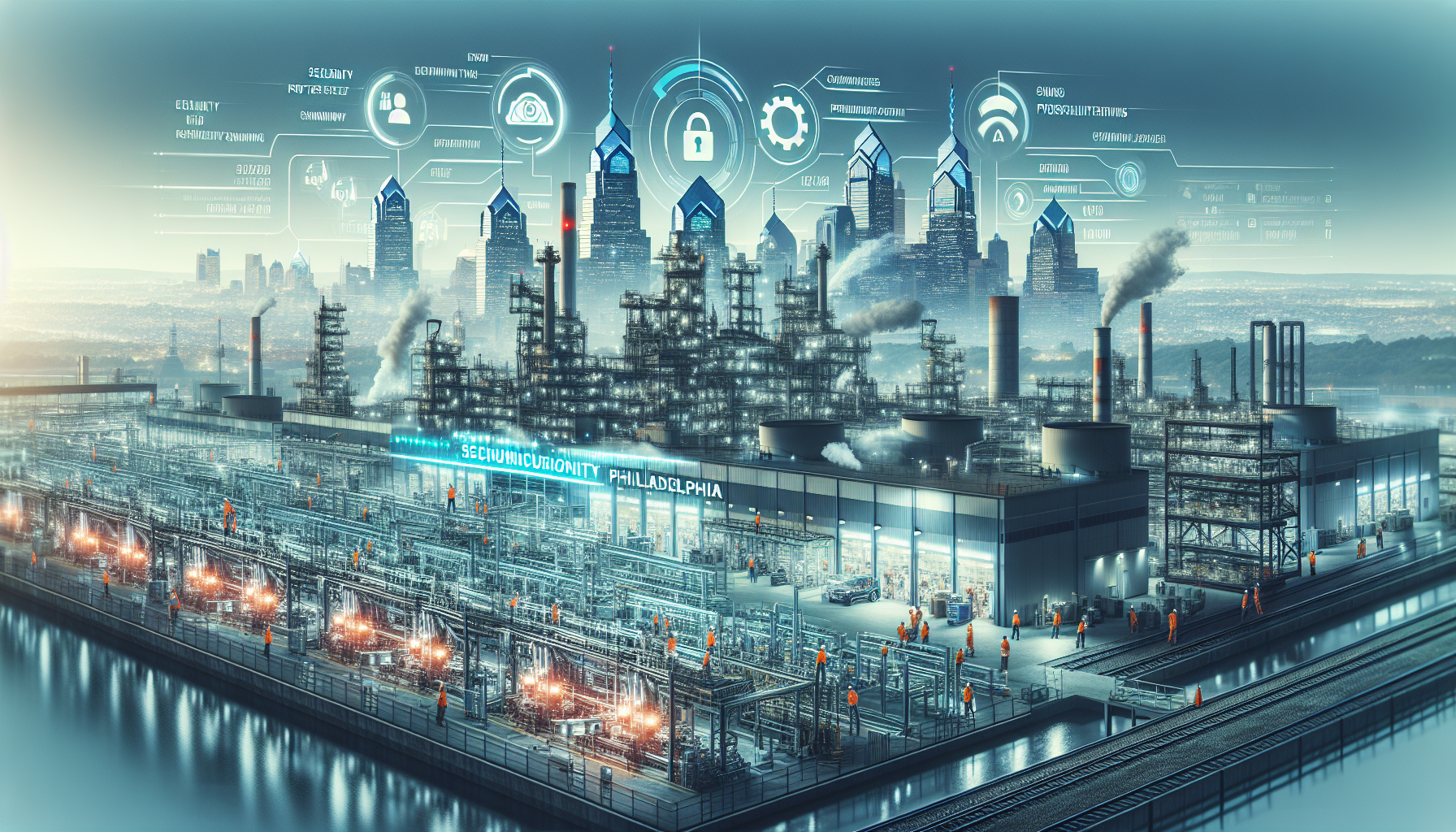
Keeping production safe and steady
The modern Philadelphia factory floor is a patchwork of robotics, legacy PLCs, brand-new IIoT sensors, and the laptops that engineers wheel between lines. Every connection is a potential doorway. When that doorway stays uninspected, ransomware, data theft, or an unexpected shutdown can walk right in. A structured vulnerability scanning schedule is the only way to know which doors are unlocked before attackers do. Yet many local manufacturers still run scans ad hoc, worried that deeper checks will jam up tightly choreographed production. The real risk is the opposite: 60 % of manufacturers reported a cyber incident last year, and each outage cost more than the hour of downtime a well-planned scan might demand. By pairing a thoughtful cadence with Philadelphia’s compliance expectations, plants can uncover weaknesses early while keeping the line moving. This breakdown explains how.
Mapping vulnerabilities on the factory floor
Vulnerability scanning in manufacturing is different from scanning an office network. Industrial control systems (ICS) may fail “closed” when probed aggressively, and a mistimed port sweep on a programmable logic controller can halt an entire batch. Understanding these nuances is step one toward a schedule that supports, rather than threatens, operational continuity.
Common security gaps in industrial control systems
Outdated firmware and operating systems still run many line controllers. Vendors sometimes stop shipping security patches after only five years, leaving decade-old systems riddled with known CVEs. We also see flat networks where shop-floor equipment shares the same VLAN as office printers, creating easy lateral movement for attackers. Finally, remote-access tools installed by third-party maintenance crews often stay active long after a service call ends. All three gaps surface quickly when a properly configured scanner sweeps for missing patches, weak segmentation, and unauthorized services.
The hidden cost of delayed detection
When vulnerabilities linger unnoticed, fixes pile up until an emergency shutdown is the only safe remediation window. That backlog quietly drains resources: insurance premiums rise, customers demand audits, and engineers spend late nights chasing anomalies instead of innovating. The Ponemon Institute notes that firms scanning monthly or faster cut breach risk in half compared with quarterly or ad hoc approaches. Translating that statistic to an automotive stamping plant in South Philadelphia means fewer unplanned line stoppages and stronger bargaining power with supply-chain partners who now expect hard evidence of cybersecurity diligence.
Choosing the right scanning cadence
How often should a plant scan? The knee-jerk answer is “quarterly,” but frequency should flex with business impact, regulatory requirements, and current threat intel. A risk-based matrix helps teams graduate from generic guidance to a schedule that fits their unique environment.
Risk-based scheduling models
We start by ranking assets on two axes: criticality to production and exposure to external networks. A high-criticality, high-exposure MES server might fall into the “weekly” bucket, whereas an air-gapped packaging controller could stay on a quarterly cycle. Include patch windows, supplier SLAs, and planned maintenance outages so scans coincide with times when fixes can be applied immediately. This alignment converts scan reports into actionable work orders rather than shelfware.
Balancing uptime with cybersecurity
Philadelphia plants often run three shifts, leaving precious little idle time. Two techniques keep scans from clashing with throughput goals. First, run credentialed, low-impact scans during production and reserve deep, device-level probes for maintenance windows. Second, stagger scans across zones; segment the network so line A scans Monday nights and line B scans Wednesdays. The operations team sees minimal simultaneous load, and security still gains weekly eyes on every asset. Real-time passive monitoring can fill gaps between active assessments, alerting teams if a new service pops up unexpectedly.
Navigating Philadelphia’s compliance landscape
Local regulations add an extra layer to scheduling decisions. While federal frameworks like NIST SP 800-82 and ISO 27001 set the baseline, Pennsylvania’s Act 73 and Philadelphia’s own critical infrastructure guidelines push manufacturers toward more frequent, documented vulnerability assessments. Insurance carriers operating in the region have started baking monthly scan requirements into cyber policies, effectively turning best practice into contractual obligation.
Key frameworks shaping local requirements
NIST’s Cybersecurity Framework, CISA’s Manufacturing Profile, and the ISA/IEC 62443 series all emphasize continuous assessment. Philadelphia’s Department of Commerce references these documents when granting tax incentives to advanced manufacturers, so proof of adherence can unlock financial benefits. Plants supplying defense or medical sectors must also meet DFARS or FDA 21 CFR §820, both of which call for documented, periodic scans and timely remediation tracking.
Leveraging Philadelphia cybersecurity partners
Several local MSSPs specialize in industrial environments. Engaging a provider like True Digital Security or a Drexel University research partnership offers two perks: tooling tuned to fragile ICS protocols and staff who know PECO’s power fluctuation patterns or SEPTA’s preferred vendor lists. Their familiarity shortens the scoping phase and reduces the chance of a scan knocking out an essential control cabinet. Keep contracts flexible so cadence can tighten temporarily during periods of heightened threat activity, such as large sporting events that historically attract opportunistic phishing campaigns.
Strengthening resilience through smart scheduling
A vulnerability scanning schedule is not a calendar exercise; it is a living risk-reduction engine. When frequency follows asset criticality, when scans sync with maintenance windows, and when local compliance nuances guide documentation, Philadelphia manufacturers gain a security posture that supports growth instead of hindering it. The next logical step is automation. AI-driven scanners already correlate CVE feeds with plant-specific configurations to suggest patch priorities automatically. As those tools mature, expect the conversation to shift from “how often do we scan?” to “how quickly can we remediate?” For now, setting a thoughtful, adaptable cadence is the surest route to fewer surprises and steadier production tomorrow.
Frequently Asked Questions
Q: What is the minimum recommended scan frequency?
At least quarterly for low-risk assets, but monthly or weekly for systems that touch production schedules or external networks. The tighter cadence reflects the rapid appearance of new vulnerabilities and the high cost of downtime.
Q: How do I avoid production disruptions during scans?
Use credentialed, low-impact scans in business hours, schedule deeper probes during planned maintenance, and segment networks so only one line is scanned at a time. Clear runbooks and engineer coordination are essential.
Q: Which regulations apply specifically to Philadelphia plants?
In addition to NIST and ISO standards, review Pennsylvania Act 73, local critical infrastructure guidance, and sector-specific rules like DFARS or FDA regulations if you supply defense or medical markets.
Q: Are automated scanners enough, or do I need manual testing?
Automated tools catch the bulk of known CVEs quickly. Periodic manual assessments still add value by identifying business-logic flaws, misconfigurations, and network pathway issues that scanners may miss.
Q: Can smaller manufacturers afford a robust schedule?
Yes. Start with open-source scanners, focus on top-critical assets, and outsource deep dives to local MSSPs on a quarterly retainer. Incremental coverage is better than none, and insurers often subsidize these efforts.